ENGIE Laborelec is conducting technical due diligence on NET Power’s supercritical CO2 power cycle. This groundbreaking technology is a potential game changer for power production, using natural gas and oxygen to generate zero-emission electricity while also capturing CO2.
The supercritical CO2 cycle is an ingenious technique to avoid both CO2 and NOx emissions, simply by burning natural gas (CH4) with pure oxygen (O2), instead of air which comprises 78% nitrogen and other gases in addition to oxygen.
This oxy-combustion process produces pure water (H2O) and pure carbon dioxide (CO2), which cycles through a turbine, a heat exchanger, and a compressor to produce power with zero emissions. At the end of the cycle, most of the undiluted CO2 is reheated in the heat exchanger and returned to the combustor to keep the cycle going. Any excess CO2 is captured in a pipeline and can either be sequestered or sold to industry.
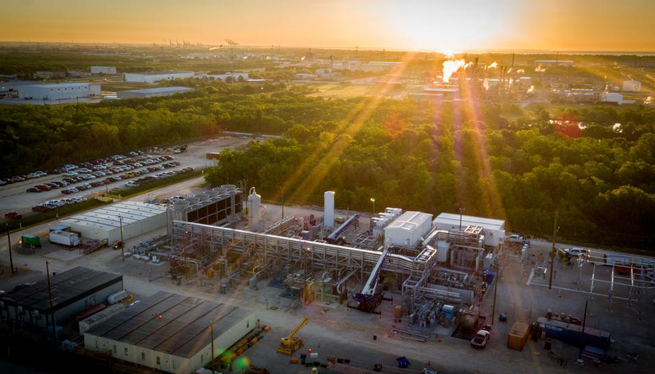
The world’s first large-scale supercritical CO2 plant
The technology, which has been under study since 2010, has reached a promising level of maturity in recent years, especially after clean energy technology company NET Power brought the world’s first supercritical CO2 pilot plant into operation in La Porte, Texas in 2018.
One of the fascinating aspects of this technology is the extreme density of the supercritical CO2 pumped through the system, meaning that the installation can be very compact and could even be built underground. Other advantages are the highly recuperative character of the cycle, minimizing natural gas consumption, and the fact that CO2 capture is part of the cycle, which is not the case in classic combined cycle power production processes.
Auditing the demonstration plant and developing a simulator
ENGIE Laborelec is now conducting technical due diligence at the La Porte demonstration facility, witnessing a series of tests and analyzing the results using data mining.
Laborelec experts are also developing a NET Power cycle simulator, which will allow variants of the cycle to be examined and benchmarked, accelerating the process of optimizing the design.
For Laborelec expert Frederiek Demeyer this is just the beginning: “We’ll also be using the experience gained on the project to evaluate whether the technology is a feasible solution for ENGIE, both technically and financially.”
Would you like to learn more about this project?