TORSO
Detecting and addressing harmful
torsional vibrations in shaft lines
Among the potential harmful conditions for turbo groups, torsional vibration is one that is generally overlooked although it can lead to dramatic failures. The issue requires special attention in today’s new normal of constantly changing grid circumstances. With TORSO, ENGIE Laborelec provides a suite of detection and protection solutions that address this issue effectively, bringing you peace of mind.
An understated risk
Although power system designs generally reduce the risk of damage due to torsional vibration to a minimum, later adjustments to the shaft line can compromise the system’s resilience. In addition, the energy transition makes for a much more dynamic grid where classic power systems interact with wind farms and an increasingly elaborate apparatus of power electronics. This could lead to excessive levels of torsional vibration in the rotating shafts or couplings, leading to fatigue and ultimately severe damage such as shaft cracking, blade loss or gearbox failure. Unfortunately, current shaft lines are not equipped to detect and mitigate this specific type of vibration.
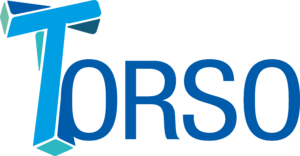
Benefits
TORSO’s automatic detection and protection functionality eliminates your worries for excessive torsional vibrations in today’s situation of constantly changing grid circumstances.
TORSO Detect, the plug-and-play version, brings TORSO’s powerful detection capabilities to your shaft line at a very limited cost.
Both TORSO Detect and TORSO Protect can be installed on most encountered types of machines, also for temporary purposes.
ENGIE Laborelec’s team of experts has more than 30 years of valuable experience in detecting harmful torsional vibration in power plant shaft lines all over the world. Our solutions and recommendations are 100% OEM-independent.
Automatic detection and immediate protection
ENGIE Laborelec’s TORSO solution addresses this issue effectively.

TORSO Detect is the low-cost plug-and-play detection system. It uses your existing array of sensors to monitor the shaft line for the presence of potentially harmful torsional vibrations. Comprehensive reporting capabilities allow you to assess the risks and decide if further analysis and protection will be needed.
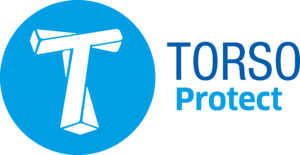
TORSO Protect is the high-end automatic protection system. We mount specific sensors at different locations along the rotor with built-in redundancy to allow precise signal processing. We also define thresholds for critical vibrations. Whenever a threshold is reached, TORSO Protect sends an appropriate alarm or trip signal to your DCS or SCADA system, protecting your shaft line from severe damage.
Bringing peace of mind
TORSO’s automatic detection and protection functionality eliminates your worries for excessive torsional vibrations in today’s situation of constantly changing grid circumstances.
The plug-and-play version brings TORSO’s powerful detection capabilities to your shaft line at a very limited cost.
Both TORSO Detect and TORSO Protect can be installed on most encountered types of machines, also for temporary purposes.
30+ years of experience
ENGIE Laborelec’s team of experts has more than 30 years of valuable experience in detecting harmful torsional vibration in power plant shaft lines all over the world. Our solutions and recommendations are 100% OEM-independent.