Webinar | How to optimize your gas turbine outage?
Maintaining gas turbines
Take control and reduce costs
Is it possible to reduce the cost of gas turbine maintenance without compromising on safety or quality? Yes, it is. In this 55-minute webinar, we tell you how.
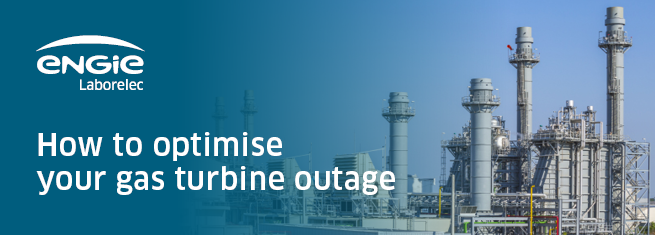
Programme
1 - Remote inspection: a viable strategy
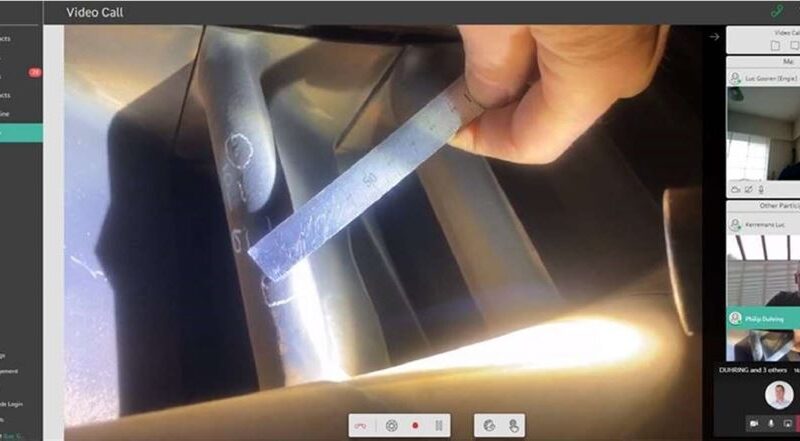
Traveling to installations or having independent experts on-site to carry out turbine inspections in the normal way is a big challenge, especially when there’s a worldwide pandemic. Remote inspections are a quick, obvious, and attractive alternative, and are not too expensive. But can they achieve everything you need, and with the same level of detail as traditional onsite inspections?
In Part 1 of this new webinar, we take a look at how remote inspections can bring significant added value, and how they can be integrated into cost-effective maintenance strategies, with real-world examples.
2 - Extending maintenance intervals: avoid the risks
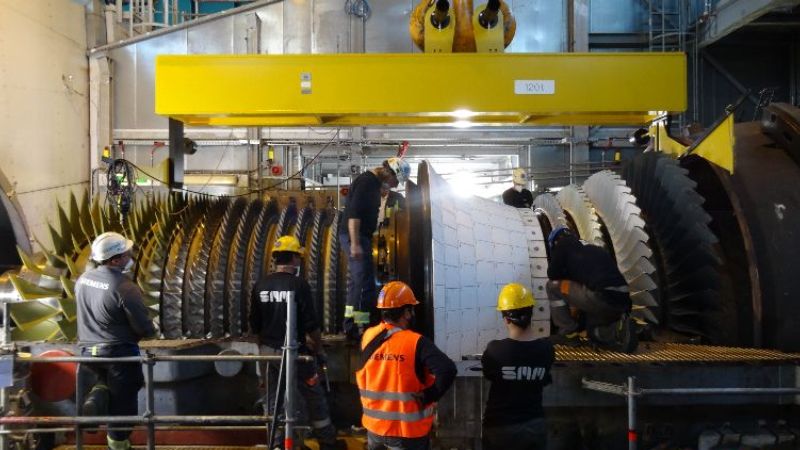
In the current market environment, there is an urgent drive to reduce costs. With spare parts representing up to 85% of all maintenance costs, extending maintenance intervals beyond the conservative schedules recommended by original equipment manufacturers (OEMs) is an approach well worth examining. But there are risks associated with it, such as unplanned stops or even failures — and insurers will need to be on board too.
In Part 2, we highlight practical examples of how risk can be assessed and mitigated, and how to satisfy OEMs and insurers.
3 - Maintenance downtime: a critical opportunity
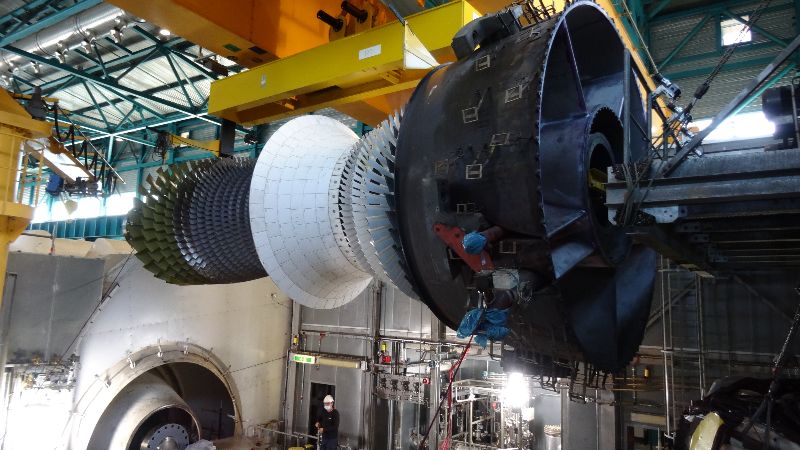
Downtime for maintenance is both a risk and an opportunity. It’s a risk because changes made during downtime could have a negative effect on process performance. It’s an opportunity because, by measuring certain process parameters before and after shutdown, modifications can be more informed and targeted. Control the risks and you can take full advantage of the opportunities to achieve better performance.
In the webinar’s final part, we share best practice on how to pro-actively identify potential risk points, minimize any knock-on performance consequences, and optimize start-up for trouble-free operation.
Want to watch the webinar?
What happens to my personal data?
This form collects a small quantity of personal information to help ENGIE Laborelec better understand the needs and areas of interest of its audience, and adapt the company’s offer of webinars, training courses and technical services. In some very limited circumstances, we may use it to contact you with carefully selected content which we think may be helpful for your business or activities. Personal data will be treated according to the ENGIE privacy statement and will be deleted after 12 months.