In the current challenging situation presented by the COVID-19 outbreak, it may be impossible for you to get external assistance on site. Remote support
may be the only viable way for you to get access to data analysis and targeted advice for your particular case.
This is where the mobile version of the Laborelec Vibration Monitoring System (LVMS 4) comes into action. The mobile system is quickly installed with the guidance of ENGIE Laborelec vibration experts, who can then provide exactly the same level of advice as they would if present on site.
The mobile LVMS4 System
ENGIE Laborelec has 10 mobile LVMS4 systems available for shipment to clients across the globe. All the systems are equipped with the hardware needed
to monitor different types of asset, including the data acquisition system, screen, cables, sensors and a wireless modem.
Easy installation video
A fully explanatory how-to video helps plant personnel to install the system. With the remote support of your ENGIE Laborelec expert the system is up and ready to make the first measurements in less than an hour.
Fully developed procedures
For every type of service, whether it’s balancing or incident analysis, ENGIE Laborelec has fully-developed procedures, with well-defined roles and responsibilities, ensuring that work can progress smoothly.
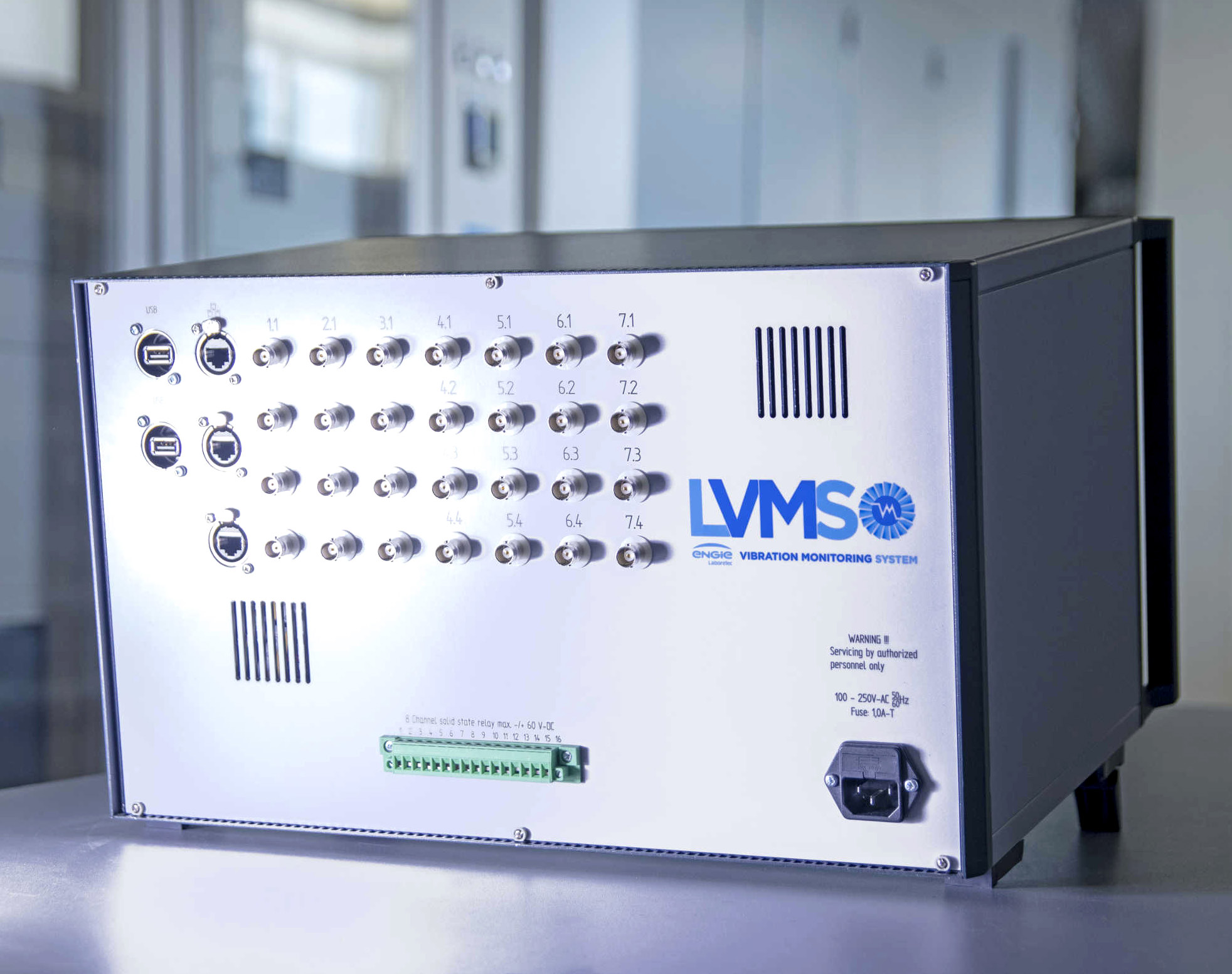
The benefits
Always available
With a 24/7 on-call system involving no less than ten ISO 18436-2 Category 3 certified experts, our availability is permanently guaranteed. Our experienced experts are ready for your call, to monitor start-up, give advice on vibration behaviour or calculate the balancing correction needed to reduce vibration amplitudes.
No wasted time on site
During overhaul and commissioning things don’t always go as expected and vibration experts often have to wait around for start-ups on site, resulting in unneeded extra cost for the client. There’s no waiting time involved in remote working, so we don’t charge it to the customer.
No travel costs
For on-site missions, the extra cost of air travel, and the time involved, represent a substantial part of the total cost. With remote support, you only pay for the expert’s time actually spent on resolving your issues.
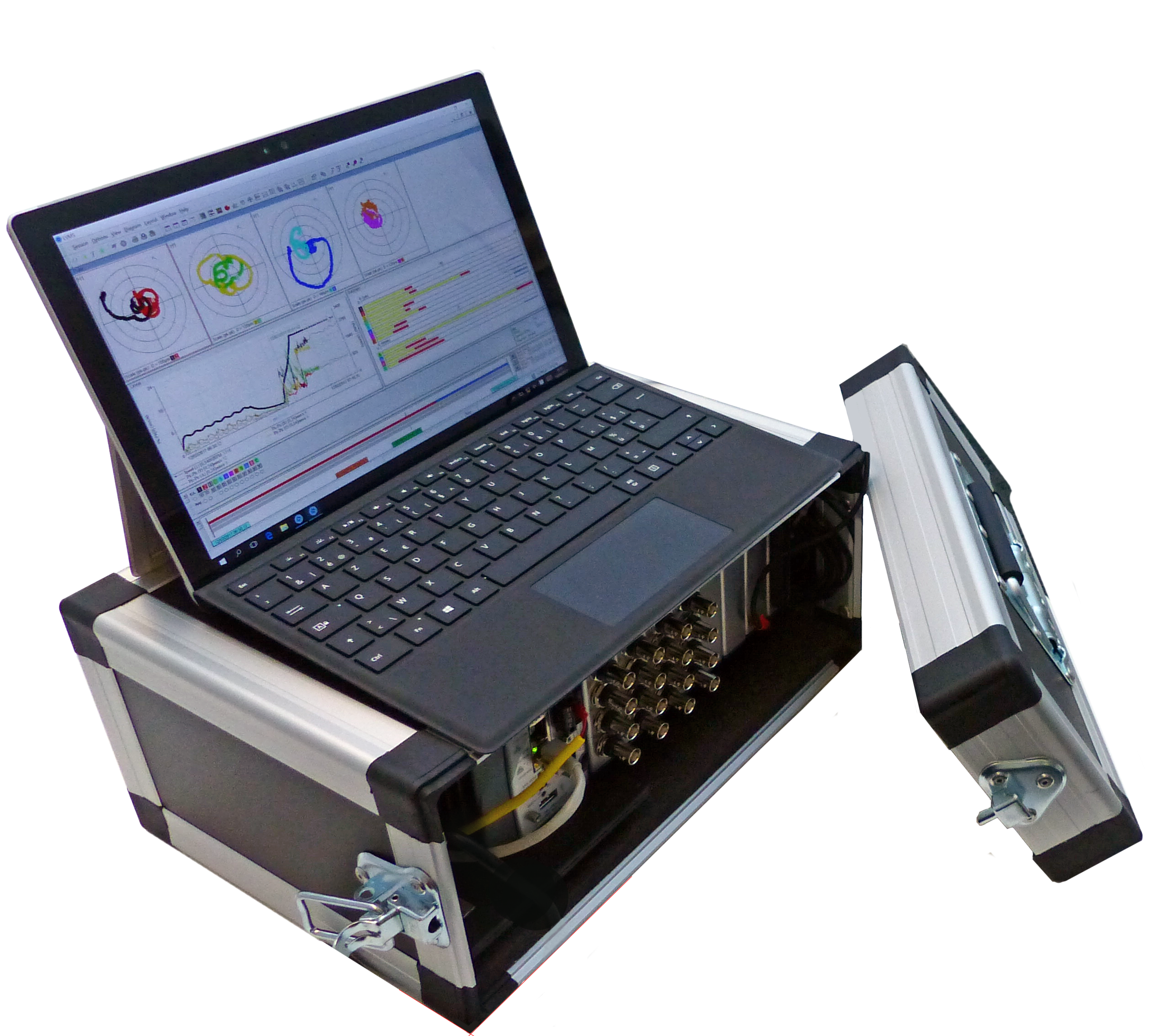
Remote services
Shipping
Our Mobile LVMS systems are fully prepared and ready for immediate shipment from our laboratories in Belgium and our offices in Santiago (Chile) and Abu Dhabi.
Installation
Our installation video is freely available on YouTube. Check it out in advance to see how easy it is to install
the system. ENGIE Laborelec is on-call 24/7 for remote expert support during installation.
Vibration analysis
Vibration behaviour is monitored and analysed by independent ISO 18436-2 Category 3 certified experts.
Dismantling
The system can be dismantled by the customer in just 30 minutes for return to ENGIE Laborelec.
24/7 EXPERT ASSISTANCE
- Our ISO CATIII experts on-call 24/7
- Long-term monitoring of asset vibration behaviour
- Immediate assistance if alarms sound
- Risk assessment in case of alarms
VIBRATION TROUBLESHOOTING
- Short term incident troubleshooting
- Independent troubleshooting
- Interpretation and analysis of incidents and phenomena
- Remote or on-site investigation
- Existing vibration monitoring system or LVMS
BALANCING
- Reducing the vibration amplitudes
- Remote or on-site balancing
- Risk/vibration reduction
- ISO 20816 zone A criteria results
- Limiting the cost of the service to the actual value
- Existing vibration monitoring system or LVMS
FLEET SCREENING
- Screening of multiple machines
- Extensive machine fleet health status
- Machine specific phenomena
- Concise reporting
- Existing vibration monitoring system or LVMS