As a gas power station operator, you are coming under increasing pressure to reduce investment and operating costs in the face of an energy market in full transition. Smart OEM-independent programs for Maintenance Interval Extension can help you achieve your targets.
Why
Cost targets are a great motivator for operators to look at the possibility of extending maintenance and reconditioning intervals for their core equipment. While OEMs offer programs claiming to do this, they usually still require key components to be renewed at set intervals, whatever their actual condition, making for an unnecessarily poor benefit-cost ratio.
However, in many cases maintenance intervals can be extended successfully without the need to renew equipment. Such smart Maintenance Interval Extension projects are taking place at an increasing number of gas power stations, with savings typically ranging between 2.5 and 7.5 M€.
What
A smart Maintenance Interval Extension project is tailored to the needs of the operator, not the OEM. It involves analyzing your installation’s operating history and investigating the actual condition of the unit.
A brief preliminary analysis will suffice to reveal the cost-saving potential of smart Maintenance Interval Extension at your site, with an indication of the expected return on investment. ENGIE Laborelec will then also carry out an in-depth investigation and support you in rescheduling maintenance as well as negotiating with your OEM and insurer.
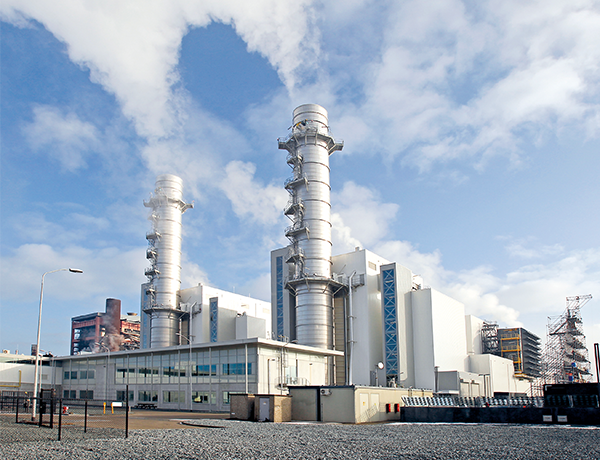
“Even though our equipment is fairly new, we were able to save 2.6 M€ thanks to smart maintenance interval extension.”
Linus WIERSMA
Maintenance Manager at Maxima Power Station, Lelystad, the Netherlands
Benefits
Since our smart Maintenance Interval Extension is tuned to meet your needs, it can maximize your cost savings.
A significant reduction in maintenance costs will improve your plant’s resilience in today’s disruptive energy market.
Smart Maintenance Interval Extension will give you enhanced insight into the health of your core equipment and increase your negotiating power in discussions with your OEM.
The wind turbine sometimes needs to be oriented to a precisely defined region for maintenance reasons or for safety reasons (f.e. Icing). With a correct north alignment, the wind turbine will be oriented correctly to the demanded position. So no time is lost and no risks are taken due to poor positioning.
Added Value
ENGIE Laborelec engages comprehensive expertise in gas turbine design and manufacturing, mechanical engineering, materials, and chemistry. We have more than 50 years of proven experience in monitoring and improving power plant operation.
We are an OEM-independent service provider, committed to improving your profitability.
How we go about it
A smart two-step investigation
We investigate your equipment by following a smart two-step approach:
Step 1: Preliminary analysis
We carry out onsite inspection and analyze the equipment’s operation and maintenance history. Then we outline the opportunities for Maintenance Interval Extension, calculating the cost of further in depth investigation as well as the expected ROI.
Step 2: In-depth investigation
We examine all the equipment’s critical components, carrying out measuring campaigns, material tests, 3D scans, modelling and calculations to assess the components’ mechanical integrity, health and expected behavior. We then make a proposal for stretching maintenance intervals without compromising equipment reliability or safety.
Implementing the changes
We also help you implement the proposed changes, making sure that the changes are accepted by your insurer and supporting you, where necessary, in discussions and negotiations with your OEM. In addition, we offer a follow-up service, carrying out reviews and inspections to ensure continuing sound operation.
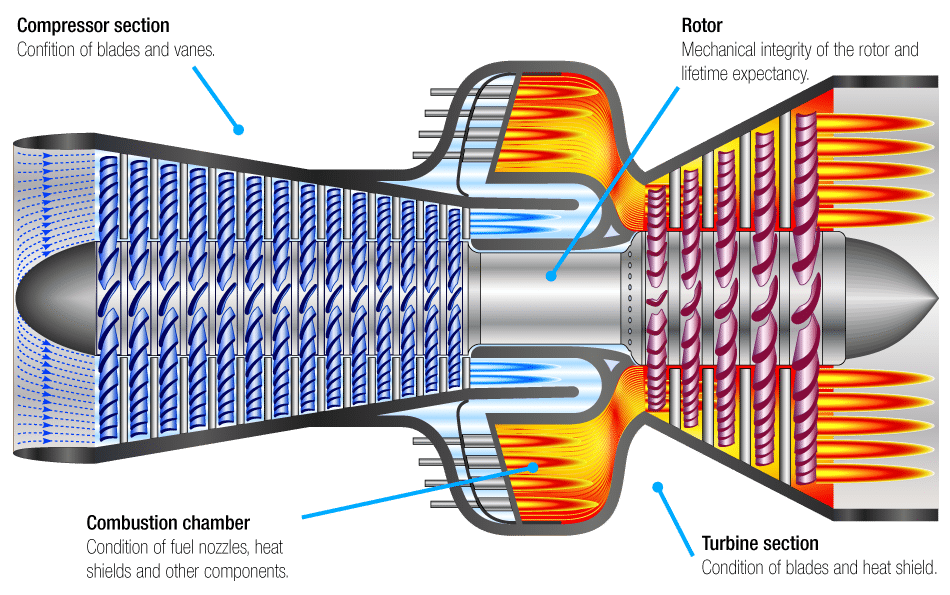