Recent innovations in air filter technology provide new opportunities for power station operators (GT or CCGT) to significantly improve plant performance and avoid compressor fouling while at the same time optimizing the filter maintenance program. ENGIE Laborelec provides comprehensive services to identify and unleash this potential.
The importance of air intake filtration
In gas-fired power stations, huge quantities of ambient air pass through the intake air filter before being used in the combustion process. It is essential that the filter system purifies the incoming air effectively, because even small concentrations of contaminants can result in compressor fouling, leading to significant power output loss over the year. Operators facing such issues can now benefit from recent innovations in air pre-treatment technology, improving power plant performance, and leading to significant cost savings. They can also grasp the opportunity to optimize filter maintenance and replacement programs, resulting in more reliable operations. For F-class machines, the impact could potentially add up to several MW of output.
Making the most of new air filter technology
ENGIE Laborelec offers comprehensive services to identify and unleash the potential for deploying state-of-the-art air pre-treatment technologies in power stations. We assess the existing filter system performance and total cost of ownership and give targeted advice for improvements, based on experience with gas turbines of the same type in similar climates and ambient conditions. Recommendations might include putting in place more appropriate and innovative technologies, modifying filter configurations, or making sure filters are always used to their full potential by optimizing the replacement schedule. Different types of ambient conditions call for dedicated air filtration solutions to guarantee optimal GT and CCGT performance.
Benefits
Optimizing the air intake will significantly improve plant performance and power output. Yearly savings between €100,000 and €400,000 per GT are not uncommon in F-class turbines.
Significant cost savings can be made by optimizing the filter maintenance and replacement programs, based on our expert field experience.
Added value
We use state-of-the-art measuring equipment for large turbine filters of all types. ENGIE Laborelec provides vendor-neutral advice, giving recommendations that are in the customers’ best interests, reducing total cost of ownership.
We have experience with all major filter and gas turbine OEMs, and comprehensive field experience in open cycle and combined cycle power plants around the world, operating in diverse ambient conditions.
How it works
Step 1: Independent testing and reviewing
We test your air intake filter elements on a test bench, measuring aspects such as pressure drop versus air mass flow and filter efficiency versus particle size. Based on the results, we develop a business case for improving performance and reducing costs. This includes a thorough analysis of operating conditions, the local contractual context for the power delivery, and the ambient conditions around the power station. The result is a dedicated, experience based, and customized set of recommendations for your specific GT.
Step 2: Upgrade assistance
We help you to validate and implement the business case; we adopt a life cycle cost approach, which also reflects the expected performance gains. ENGIE Laborelec assists in compiling the necessary specifications, taking account of system compatibility constraints. We subsequently assist in evaluating and comparing the incoming vendor proposals. Alternatively, we are also happy to organize delivery and onsite installation if required.
Validating manufacturer claims
ENGIE Laborelec also carries out independent tests on filter sets at the time of purchase to validate their initial performance. We can also use operational data to monitor the impact of a filter upgrade on compressor efficiency and pressure drop to check how performance compares with manufacturer guarantees over the GT’s entire life.
Worldwide experience
We have experience with all major filter and gas turbine OEMs, and with most types of machines. In addition, we have comprehensive field experience in air filter optimization at more than 40 sites (and 100+ GTs), operating in diverse ambient conditions around the world. All our services benefit from the vast worldwide network of contacts we have within power plant operations and maintenance teams, evaluating and troubleshooting issues at hand.
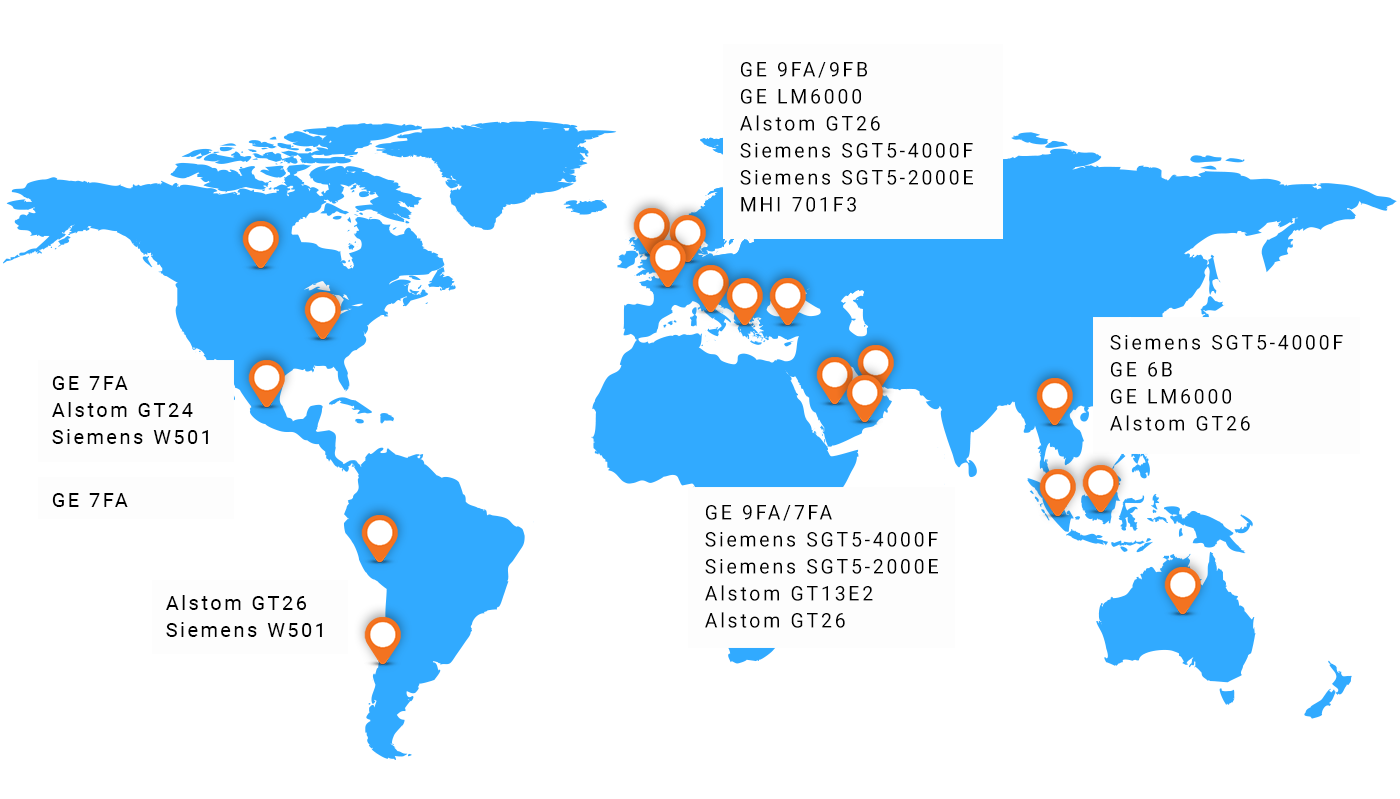
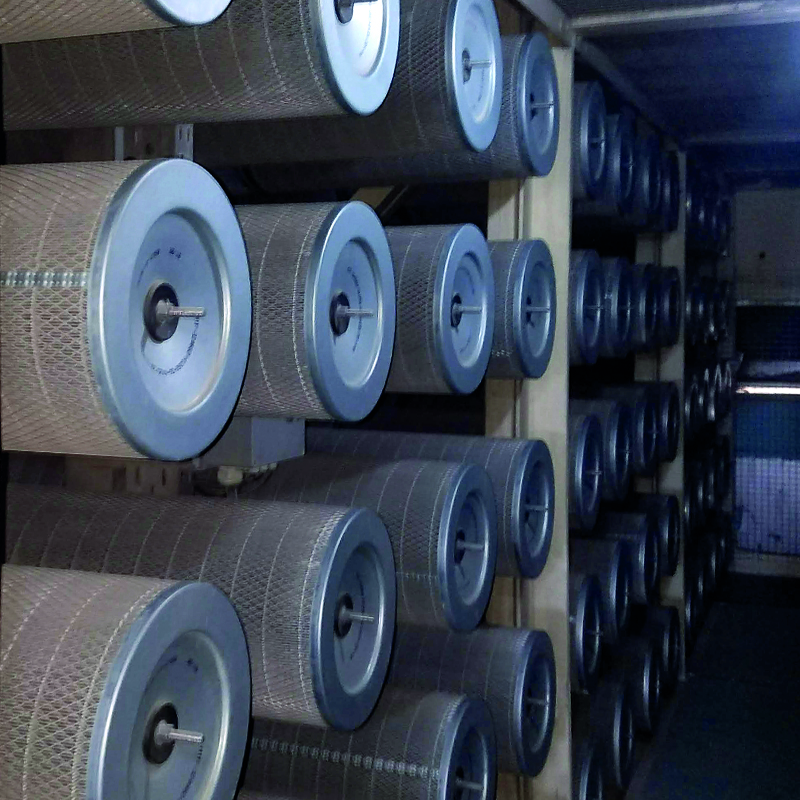
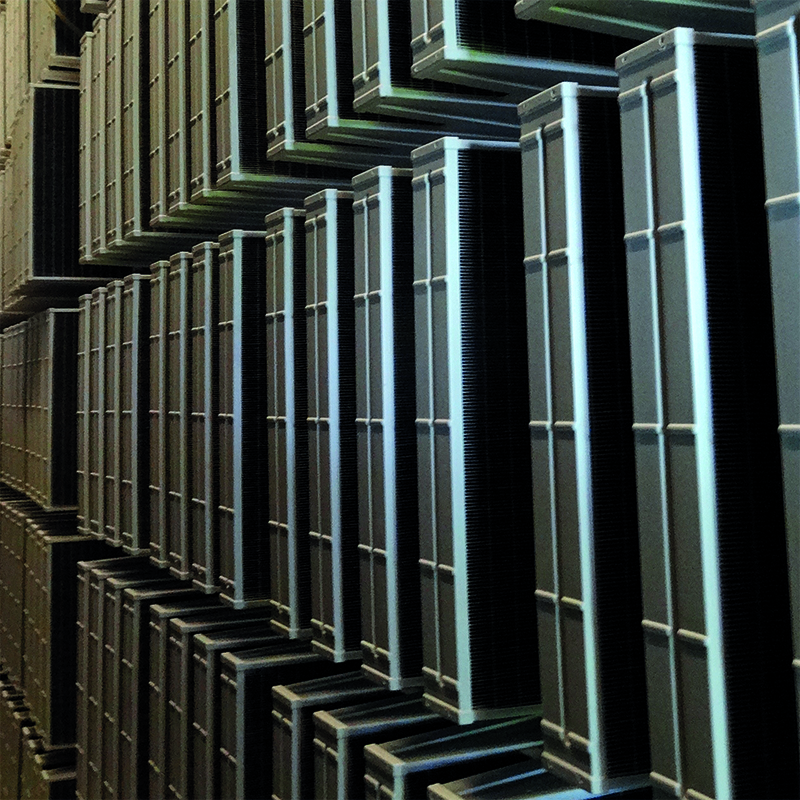