Getting clear asset management scenarios
Once the different catalyst samples have been tested in our lab, and with a clear picture of the installation’s non-catalyst performance, it is possible to estimate the future evolution of the various catalyst layers and develop an optimal catalyst asset management plan. Using our proven in-house model based on 20 years’ experience, ENGIE Laborelec carries out a clear assessment of the remaining catalyst lifetime beyond OEM guarantee, and proposes the most cost-effective catalyst management plan. In line with our focus on achieving the lowest possible total cost of ownership, we identify all the potential O&M improvements that can further postpone the end of life of the catalyst.
Independent catalyst lifetime assessment
The model we use takes as input the catalyst test results and the results of the SCR plant inspection, as well as data related to its design, operation and maintenance history. Using these data, we estimate how the individual catalyst layers will evolve over time, so that we can give a clear indication of the remaining catalyst lifetime, beyond OEM guarantee.
For operators with multiple SCR facilities, there is a clear economic interest in managing catalyst ageing at fleet level. We take these aspects into consideration, always with the aim of providing maximum value at the most optimal cost.
Independent SCR asset management planning
Various scenarios are possible to manage catalyst lifetime. Without the biased viewpoint of catalyst or regeneration companies, ENGIE Laborelec can independently evaluate and compare the different asset management scenarios and guide the O&M team towards achieving the lowest possible total cost of ownership.
The formulation of effective catalyst management plans is not the only interesting result to emerge from the modelling exercise. The parallel collection of data related to the catalyst and data related to the overall state of the installation also makes it possible to identify improvements to operation and maintenance. Typical examples of such improvements are:
- Improvement to the cleaning system.
- Tuning of ammonia injection.
- Solutions to erosion or bypass issues.
Because of our independence from OEMs and regeneration companies, you can be assured that our experts will always propose cost-effective O&M improvement actions whenever possible, in preference to costly new catalysts or regeneration, as the best path to optimizing total cost of ownership.
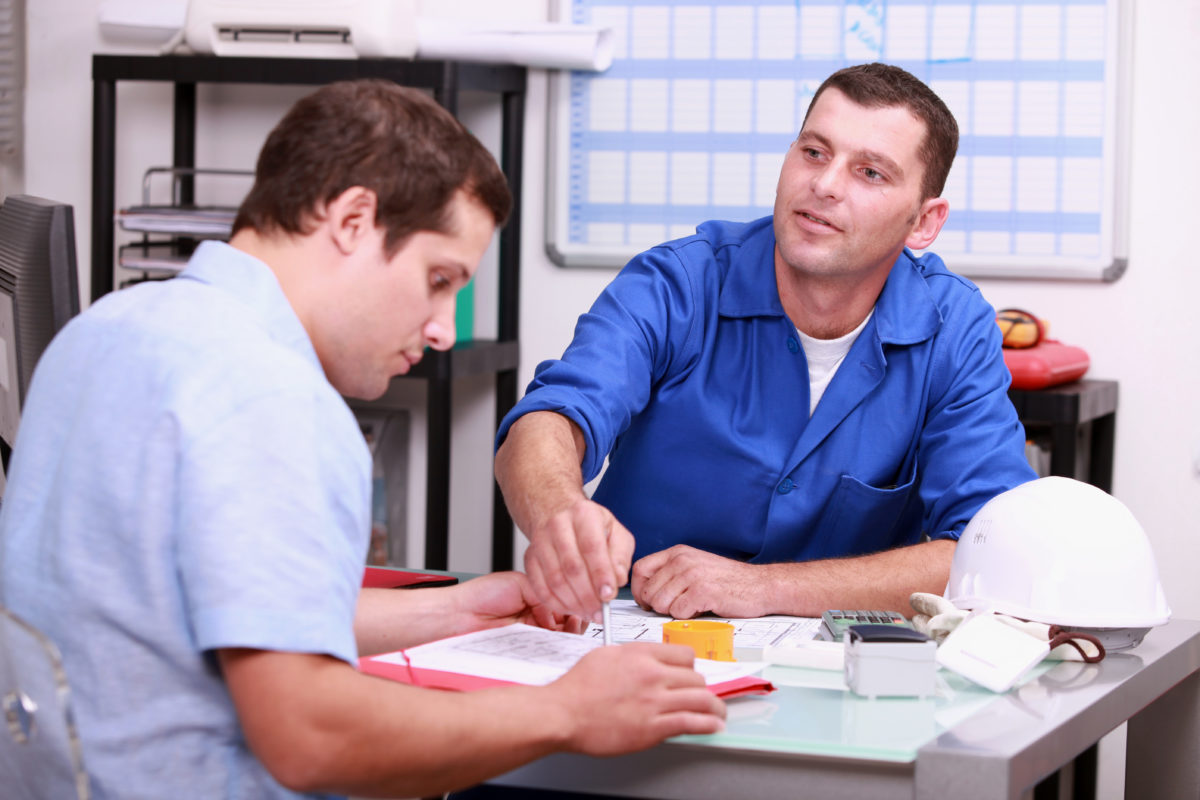