Preventing damage through remote water-steam chemistry supervision
Chemistry deviations in the water-steam cycle can cause significant damage. They often go unnoticed or are not properly addressed, leading to unplanned outages and high costs. CHESS, ENGIE Laborelec’s CHEmistry Supervision Service, supports plant operators by identifying potential chemistry issues before they can do serious damage, and provides expert advice on remediation and prevention.
WHY - Chemistry issues staying under the radar
Chemistry issues are known to be involved in most boiler tube failure mechanisms, as either the main contributing factor or as catalysts in the degradation process. Sadly, these chemistry deviations stay mostly under the radar or are rarely signaled. As a result, the signs are often ignored by operators or not properly addressed. Over the l ong term, this could increase the plant’s general corrosion rate and cause deposition phenomena to occur. It is therefore essential to assure state-of-the-art follow-up with proper expert guidance.
WHAT - Signaling and addressing chemistry issues
CHESS helps power plants avoid costly downtime and repair works by signaling potential water-steam impurity issues whenever they occur. The service is backed by a cloud-based platform which automatically aggregates and analyzes plant DCS data, calculating chemistry KPIs and signaling deviations. ENGIE Laborelec chemistry specialists monitor these KPIs, further analyze the data where needed and provide expert advice on how to address the issues. They also give on-site support to follow up action lists, carry out actions and conduct on-the-job operator training.
Benefits & added value
ENGIE Laborelec chemistry experts deliver a continuous supervision service, remotely monitoring the water-steam cycle chemistry using intelligent digital tools. They provide proactive support in the event of a chemistry deviation. This means a more rapid response to chemistry incidents, leading to long-term improvement. Monthly chemistry KPI reporting also contributes to better risk management.
Unplanned shutdowns can cost up to €100,000 a day, while losses due to a major chemistry incident can run into the millions. Better chemistry management avoids all this. As well as preventing unplanned outages, top-class chemistry management reduces the need for chemical cleaning, generating recurrent savings of several thousand euros per year.
Regular exchanges with plant operators combined with yearly on-site visits by ENGIE Laborelec experts contribute to greater understanding and awareness of chemistry-related issues by power plant staff.
How it works
Every five minutes, ENGIE Laborelec processes data from plant on-line water-steam cycle analyzers. Whenever a chemistry deviation requiring action is detected, an ENGIE Laborelec expert contacts plant operators with feedback and guidance. CHESS uses dedicated logic and algorithms to monitor the chemistry by cross-linking the various parameters. This sets off Key Performance Indicators (KPI) assuring early detection of incidents and reporting. CHESS also analyzes chemistry alarm levels relating to the actual plant operational mode, avoiding reacting to non-relevant alarms and offering a more efficient follow-up of plant cycling. This intelligent data processing layer is derived from experience with past plant start-ups. The CHESS package also includes CLASH (Condenser Leakage Automatic Shutdown), which avoids severe damage by assuring an automated trip in the event of a major condenser leakage. CLASH implementation is tailored to the individual power plant, using selected online analyzer threshold values to ensure that the condenser leakage indicator is fully reliable. This indicator is used to trigger the trip signal in the DCS.
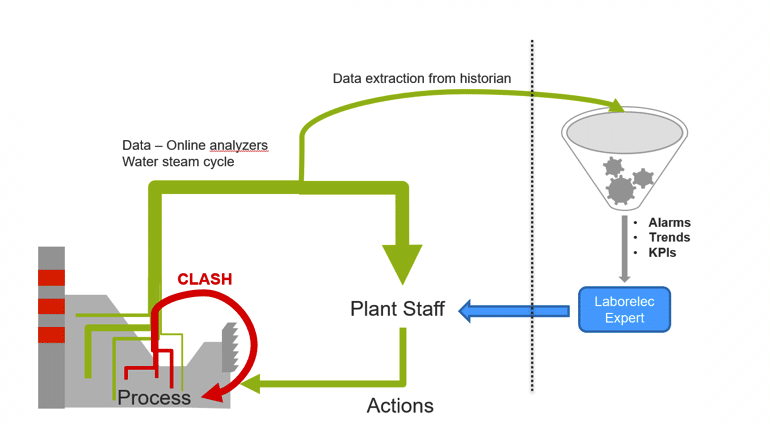
HOW DO WE IMPLEMENT CHESS?
CHESS can be put into operation at any power station or power generating industrial site. The continuous remote monitoring is a three-step process:

CASES FROM THE FIELD
The rhythm of the sea
At a power plant in France, the DCS was intermittently signaling a high sodium concentration in the water-steam cycle condensate. While increased sodium concentrations could indicate a condenser leakage, plant operators weren’t alarmed in this instance because the sodium levels always came back to normal after about six hours. ENGIE Laborelec’s expert, however, analyzed the CHESS KPIs. This allowed him to conclude that there was indeed a minor condenser leakage. It was the influence of the tide on water salinity that was leading to the unusual six-hour intervals.
He also concluded that the salt contamination was sufficiently limited that it could be dealt with first through drum blowdown. So, he was able to advise against an immediate shutdown, allowing the leakage search to be postponed until the next planned outage.
Costly intervention and an unplanned outage were avoided thanks to CHESS.
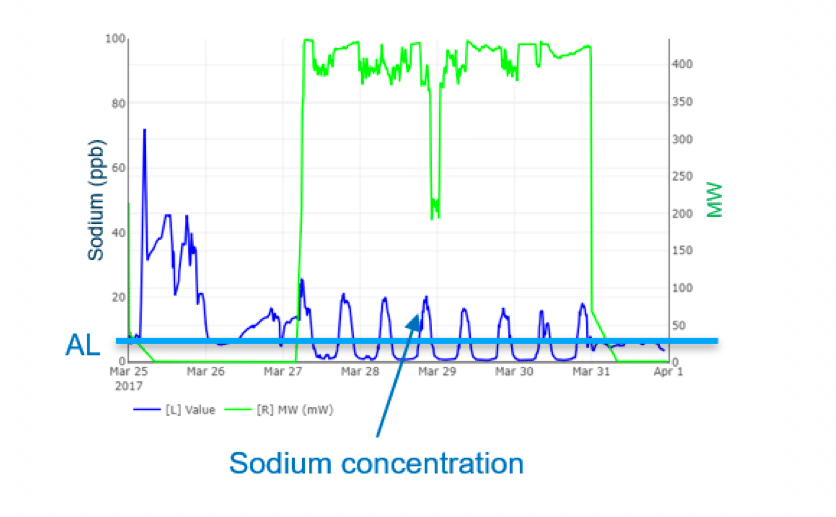
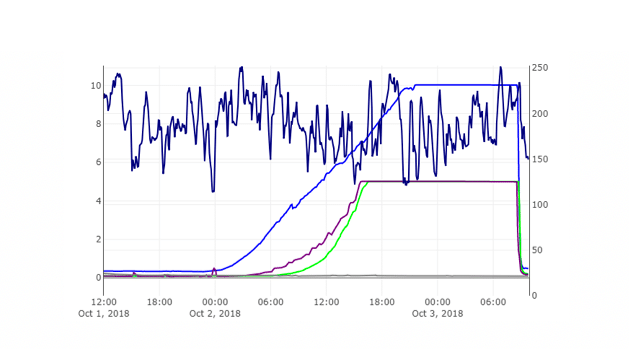
Avoiding counterproductive action
The purity and treatment measurements of a power plant in Italy had rapidly increased to above alarm levels. While this would normally lead operators to open the blowdown, ENGIE Laborelec was able to demonstrate that this was the wrong action to take. Analysis and cross-checks of the CHESS KPIs revealed the nature of the contamination: there was a problem with the caustic leaching in the production of demineralized water. This meant that any increase in the makeup water flow from the demineralization tank would have been counterproductive.
It was therefore necessary to first correct the caustic leaching problem, then drain and refill the demineralization tank, and finally open the blowdowns to evacuate the contamination. A clear example of how the CHESS service helps operators to make the right decisions.